AkzoNobel's Cool Chemistry® Coil Coating System
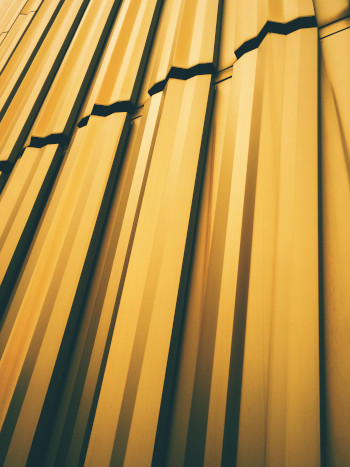
Exceptional Durability
COOL CHEMISTRY® is a silicone modified polyester coil coating system that combines the exceptional durability of Akzo Nobel's CERAM-A-STAR® with the cooling power of organic, inorganic, and ceramic pigments. It also provides exceptional long-term exterior weathering performance, long term resistance to chalking and fading, and offers superior resistance to moisture and UV exposure, with excellent flexibility and abrasion resistance.
It features superior color stability, chalk resistance, fade resistance and gloss retention. It is resistant to scratches and abrasions, which is a big bonus during transit, handling, and installation - particularly in hot weather. It also has excellent resistance to smudges, dirt pickup, and atmospheric stain.
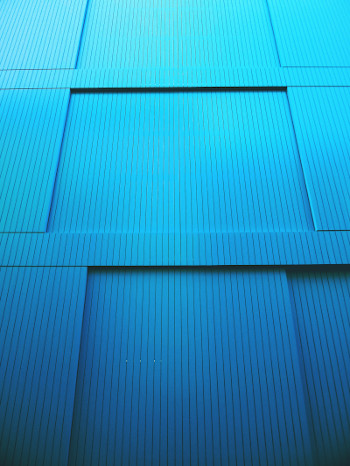
Reduced Energy Usage
COOL CHEMISTRY® will help to reduce the energy use associated with cooling a structure. When used on metal roofing, the result is a sustainable building material that can help lower air conditioner costs, reduce peak energy demand, and help to mitigate urban heat island effects.
It is designed to meet Energy Star® guidelines, in addition to other local, regional and federal code requirements for energy efficient building products.
Coatings have been thoroughly tested using both real life conditions and accelerated testing methods to achieve the most comprehensive and reliable results.
Stealth Black
Burnished Slate
Cocoa Brown
Charcoal
Forest Green
Emerald Green
Burgundy
Barn Red
Bright Red
Regal Blue
Hawaiian Blue
Copper Penny
Polar White
Lightstone
Sahara Tan
Ash Gray
*Actual colors may vary from samples shown. Actual color chips available upon request.
Film Properties | Test Methods & Descriptions | CERAM-A-STAR® 1050 | ||
---|---|---|---|---|
SUBSTRATE | Hot Dipped Galvanized Galfan & Galvalume* | Aluminum | ||
Dry Film thickness | ASTM1 D1400, D1005, D4138 (NCCA2 II-13,14,15) |
0.20 - 0.25 Mils Primer 0.70 - 0.90 Mils Topcoat |
0.20 - 0.25 Mils Primer 0.70 - 0.90 Mils Topcoat |
|
PHYSICAL PROPERTIES | ||||
60° Specular Gloss: | ASTM D523 | 35% | 35% | |
Pencil Hardness: | ASTM D3363 (NCCA II - 12) Eagle Turquoise Pencil |
"F" - Minimum | "F" - Minimum | |
Flexibility: T-Bend |
NCCA II - 9 |
2T - No Tape-Off |
2T - No Tape-Off |
|
Mandrel Bend |
ASTM D522 180° bend around 1/8" mandrel | No Tape-Off | No Tape-Off | |
Adhesion: | ASTM D3359 (NCCA II - 5) Reverse Impact Cross Hatch |
No Adhesion Loss | No Adhesion Loss | |
Reverse Impact: | ASTM D2794 (NCCA II - 6) 80 inch-pound impact with a 5/8" steel ball or = 2000 x decimal steel, thickness in inches |
No Adhesion Loss | No Adhesion Loss | |
ABUSE TOLERANCE | ||||
Abrasion Resistance: Falling Sand |
ASTM D968, Liters to expose 5/32" area of substrate |
30 Liters Per Mil of Film |
30 Liters Per Mil of Film |
|
Transit |
Based on topside to backer contact in transit after painting | Acceptable | Acceptable | |
Mortar Resistance: | AAMA3 605.2 (24 Hour Pat Test) | No Effect | No Effect | |
Detergent Resistance: | ASTM D2248 3% @ 100°F, 72 Hours | No Effect | No Effect | |
RESISTANCE TO CORROSION, CHEMICALS & POLLUTION | ||||
Acid Pollutants
10% Muriatic Acid
|
Per ASTM D1308, Proc.6.2: 24 Hours |
No Effect |
No Effect |
|
20% Sulfuric Acid |
24 Hours | No Effect | No Effect | |
70% Nitric Acid Vaports |
AAMA 605.2,ASTM G87 (30 Minutes | <5 dE Color Change6 | <5 dE Color Change6 | |
Kesternich Test |
SO2 Cyclic Test, 2 Litres | 10 cycles5 | 10 cycles5 | |
Alkali Resistance: Sodium Hydroxide |
ASTM D1308 10%, 25% (1 Hour) |
Minimal Effect |
Minimal Effect |
|
Salt Fog: | ASTM B117 5% Salt Fog @ 95°F | 1000 Hours4 | 3000 Hours4 | |
Humidity: | ASTM D2247 100% Relative Humidity @ 100°F | 1500 Hours7 | 1500 Hours7 | |
WEATHERING PROPERTIES | ||||
Accelerated Weathering: | ASTM D822, G152, G153 Weatherometer | 2000 Hours | 2000 Hours | |
ASTM D2244 Color | <5 dE Color Change6 | <5 dE Color Change6 | ||
ASTM D4214 Chalk | Maximum #8 | Maximum #8 | ||
EMMAQUA Testing: | Per ASTM D4141 | Superior Results Superior: Maximum |
Superior Results Superior: Maximum |
|
Exterior Weathering: Florida Exposure |
ASTM D2244 Color |
<5 dE Color Change6 |
<5 dE Color Change6 |
|
10 Years @ 45° South |
ASTM D659 Chalk | Maximum #8 | Maximum #8 | |
Film Erosion |
AAMA 605.2 | Less than 20% film loss | Less than 20% film loss |
1American Society Testing and Materials.
2National Coil Coaters Association.
3American Architectural Manufacturers Association.
4Less than 1/8" creep from scribe. No more than few #8 blisters.
5No objectionable color change.
6Hunter d (delta) E color difference units.
7No more than few #8 blisters.
*CERAM-A-STAR® 1050 is a trademark of Akzo Nobel Coatings, Inc.